1. 서 론
2. Micromix 연구 동향
2.1 Micromix 원리
2.2 형상 인자별 연구 결과 분석
2.3 Multi-nozzle Micromix combustor
2.4 Micromix combustion instabilities
3. Micromix 연소기 실용 사례
4. 결 론
1. 서 론
2017년 IEA에서 발간한 세계 에너지 전망 보고서에 따르면 2040년까지 에너지 수요는 꾸준히 증가할 것으로 예상된다[1]. 늘어나는 에너지 수요를 대응하기 위해 안정적이고, 효율적이며, 확장이 용이한 에너지 시스템인 가스터빈의 역할이 더욱 중요해질 것으로 기대된다. 그러나 천연가스 등 화석연료를 주 연료로 사용하고 있는 가스터빈의 연소 과정은 질소산화물(NOx) 및 일산화탄소(CO) 등 오염물질을 배출하게 되며, 이 오염물질은 지구온난화와 같은 환경오염 문제를 일으키게 된다.
환경문제 대응을 위한 가스터빈 제조사들은 오염물질 배출 저감을 목적으로 기존의 비예혼합 연소 시스템에서 희박 예혼합(lean pre-mixed, LPM) 연소기술로 전환하였다. 이후 LPM 연소기술을 기반으로 dry low NOx(DLN), enhanced vortex(EV), Perforated-plate(PP) 그리고 micromixer(MM) 버너 등 새로운 형태의 연소기를 개발하고자 노력하고 있다. 하지만 오염물질의 배출 규제가 더욱 강화됨에 따라 최근에는 수소 연소에 주목하고 있다. 수소는 무탄소 연료로 환경친화적이며, 지역적 편향 없는 보편적인 에너지원으로써 지속 가능한 물질이다. 기존의 가스터빈 연료와 특성 차이는 있지만, 이러한 장점을 이용하기 위해 가스터빈에 수소 및 수소 혼합연소를 적용하기 위한 많은 연구가 진행되고 있다.
차세대 연료로 각광 받고 있는 수소 연료는 DLN 연소기와 같이 LPM 연소 시스템이 적용되었을 경우, 수소의 연소특성으로 인해 발생할 수 있는 기술적 문제들이 보고되고 있다. 높은 반응성으로 인해 발생할 수 있는 역화(flashback), 낮은 자연발화 온도 및 짧은 점화지연시간으로 나타나는 자연점화(Autoignition) 등이 해당한다. 또한, 높은 단열 화염 온도 역시 문제가 될 수 있는데, 이는 질소산화물 배출량의 증가로 규제 준수를 어렵게 한다[2]. 이러한 문제를 극복하기 위해 Dry low-NOx Micromix 또는 Micro Mixer type의 연료 노즐을 다수 적용한 Multi-jet 형식의 연소기 개발 연구가 진행되고 있다[3]. Micromix(이하 MM)의 개념이 가스터빈 엔진에 적용된 개념을 Fig. 1에 제시하였다.
MM 연소 시스템은 인젝터의 연료 주입구 크기가 평균 1 mm 이하로 구성되어 있으며, 수소 또는 수소 혼합연료를 여러 노즐을 통해 연료 제트를 공기와 교차로 혼합시킨다. 노즐의 소형화와 소형 화염구에서의 반응물 체류 시간을 짧게 하여 NOx를 획기적으로 감소시킬 수 있는 것으로 알려져 있으며, 수소 연소의 문제 중 하나인 역화의 위험을 피할 수 있는 장점이 있다[4].
수소 전소 및 혼소에 효과적일 것으로 판단되는 MM 연소 시스템은 수소의 연소 특성과 오염물질 배출제어를 위해 반응속도, 혼합 성능 그리고 체류 시간 등 이상 세 요소를 고려하여 연구가 진행되고 있다. 반응속도는 가스터빈의 사이클 연소 과정 중 환경 조건인 온도와 압력의 영향을 받으며, 이를 최적화하면 질소산화물 배출을 감소시킬 수 있으나 가스터빈의 효율을 낮추는 문제가 발생한다. 혼합물을 예혼합 수준으로 높이게 되면 NOx 배출은 낮아지지만, 가스터빈의 작동 조건에 따라 역화에 대한 위험이 증가한다. 또한, 확산형 화염을 이용하여 질소산화물 배출을 제어하기 위해서는 높은 생성속도를 제한하는 최적화된 혼합 능력이 필요하며, 수소 연소 시 고온영역에서의 반응물의 체류 시간이 길어질수록 NOx의 배출량이 증가한다[5, 6, 7]. 이상 3가지 요소들을 고려했을 때 MM 연소 시스템은 연소기의 type과 전체 형상에 따라 최적화가 필요한 것으로 보인다. 다음 Table 1 은 MM 연소 시스템 최적화를 위한, 고려 되어야 하는 인자 및 연소 불안정성 등 연구 중인 MM 연소기에 대해 정리한 것이다.
Table 1.
References for micromix combustor
Parameters | MM system type | |
Pre-mixed | Non-Premixed | |
Fuel inlet diameters | [12],[13] [18] | [14],[15][16],[17] |
Fuel inlet & nozzle shape | [19],[20] [21],[22] [23],[24] [25] | - |
Number of fuel inlets | [26] | [27] |
Bluff body & baffle | [28],[29] [30],[31] [33],[34] | [32] |
Combustion instability | [44],[45] [46],[47] [48],[49] | - |
Multi-nozzle micromix combustor | [8],[36] [37],[38] [39],[40] [41],[52] [53] | [42].[43] [50],[51] [54] |
본 연구에서는 이를 바탕으로 역화와 같은 수소 연소 특성 제어와 낮은 NOx 배출량을 위한 연소기 형상 설계에 영향을 미치는 인자들에 대해 연구 사례를 분석하고자 한다. 특히, 저탄소 배출의 차세대 연료로 각광 받고 있는 수소 연소에 있어 가장 적합하다 평가되는 MM 연소 시스템에 대한 연구 동향을 확인하고자 한다. 이를 위해 주로 연료 주입구 직경, 노즐 및 주입구의 형상 등 MM 연소에 영향을 미치는 형상 인자에 대한 연구를 분석하고, MM 연소기술에서 나타날 수 있는 연소 불안정성을 확인한 후, 차세대 가스터빈 엔진으로써의 적용을 위해 연구개발 되고 있는 MM 연소 시스템에 대한 특징을 소개하였다.
2. Micromix 연구 동향
2.1 Micromix 원리
MM 연소 시스템은 연료와 산화제가 microscale로 혼합되는 버너의 유형이다. 기존의 단일 화염 대신 매우 작은 화염을 통해 터빈 연소기 내부의 열 방출을 분산시키기 위한 것으로 튜브 내부에서의 화염 고정 위험을 완화하며, 화염 영역에서의 충분한 열을 제거하고, 화염이 내부로 전파될 때 국지적으로 소멸시키는 특징이 있다. 이는 수소 또는 수소의 함량이 높은 연료를 사용하는 가스터빈 운영과 질소산화물(NOx) 배출량 저감에 대응하기 위해 고안되었다. Fig. 2에 널리 알려진 두 가지의 형태의 MM 버너 개념도를 제시하였다. Fig. 2(a)는 예혼합 형식의 기본적인 MM 버너 형태로 전면과 후면 plate 사이에 여러 개의 밀리미터 크기의 직선 튜브를 배치하여 직선 튜브 입구에는 산화제를, 직선 튜브 측면에는 마이크로 홀을 통해 기체 연료를 주입한다. 각 튜브에서 공급된 산화제와 마이크로 홀을 통해 공급된 연료 가스가 혼합 후 연소 되는 예혼합 방법이다[8]. Fig. 2(b)는 독일의 아헨대학교에서 1990년부터 연구 개발한 비예혼합 형식의 MM 버너이며, 현재 상용화된 방법 중 하나이다. NOx 배출량을 크게 줄일 수 있는 수소 micromix 확산 연소방법으로써, 1 mm 이하의 미세한 주입구를 통해 여러 개의 작은 화염을 생성하고, 작은 화염이 공기와 빠르게 혼합됨에 따라 반응물의 체류 시간이 짧아져 NOx 배출을 저감 시키는 원리이다[9, 14]. 여기서 두 형태의 공통점은 화염 소형화를 위해 microscale의 연료 주입구로부터 발생하는 제트(jet) 현상을 활용한다는 점이다. 이는 MM 연소기의 기본이 되는 lean direct injection(LDI) 방식을 적용한 것으로 빠른 혼합을 위해 연료가 여러 위치에서 산화제에 주입되며, 이는 빠른 반응성을 가지는 수소의 연소 특성 문제인 역화를 방지하는데 적합하다. 또한, 교차 유동(cross-flow)을 포함한 선회(swirl), 반경(radial) 및 축류 유동(axial) 및 동축 유동(co-flow) 등 다양한 혼합 방식을 적용할 수 있다[10, 11].
2.2 형상 인자별 연구 결과 분석
2.2.1 연료 주입구 직경에 따른 영향
연료 주입구 직경은 연료-산화제 혼합 등에 영향을 미치는 것으로 알려져 있다. Araoye 등은 예혼합 타입의 단일 MM 노즐을 이용하여, 연료 주입구 직경 변화에 따른 혼합 성능에 대해 조사하였다[12]. 튜브 길이 L=10D와 일정한 유량으로 주입되는 연료 주입구 직경을 1 mm부터 0.2 mm 간격으로 감소시켜 수치연구를 진행한 결과, 직경 0.2~ 0.35 mm 사이에서 90% 이상의 높은 혼합 성능을 확인하였다. 이는 연료 주입구의 직경 감소가 산화제와 혼합되는 연료의 분사속도를 증가시켜 혼합에 영향을 주지만, 연료 주입구의 직경 변화의 영향보다는 산화제와 연료의 운동량 비율이 혼합에 있어 더 큰 영향을 미치기 때문임을 확인하였다.
Cha와 Hwang은 연료 공급 주입구 직경의 변화에 따라 노즐 주위 발생하는 재순환영역의 크기와 연소 특성 간의 영향을 분석하였다. 채널 길이 50 mm의 MM 예혼합 단일 노즐을 대상으로 연료 주입구 직경을 2 mm에서 0.5 mm 간격으로 변화시켜 연소 특성을 확인하였다[13]. 수치해석 결과, 노즐의 직경이 감소하면서 재순환 유동의 크기가 감소하고, 온도분포의 고온영역이 축소되면서 연료 노즐로부터 떨어져 화염이 형성되는 경향을 확인하였다. 이로부터 Cha와 Hwang은 강한 재순환 유동을 형성하는 것이 안정적인 연소 화염이 형성될 수 있음을 확인하였고, 연료 주입구 직경을 2 mm 이상으로 설정해야 함을 보고하였다.
Funke 등은 산업용 가스터빈에 적용할 목적으로 비예혼합 타입의 연료 주입구 직경 0.84 mm를 가지는 GTCP36-300 APU를 이용하여 연소 특성을 관찰하였다[14]. 비교군이 되는 참고문헌 15에서 사용한 항공용 연료 주입구 직경 0.3 mm의 실험 결과와 비교하였으며[15], 0.84 mm의 노즐을 사용하게 되면, 연소기에서 발생하는 열 에너지의 총량을 나타내는 노즐당 열 에너지 출력(thermal power output)이 0.3 mm의 직경을 가진 노즐보다 약 390% 증가한 것을 확인하였다. 또한 모든 작동 조건에서 NOx 배출량은 4.0 ppm 미만이었으며, 화염 안정성에서도 비교군과 같이 소형 화염을 나타내는 것을 확인하였다. 직경 및 출력의 증가에도 낮은 NOx 배출량과 화염 소형화를 이룰 수 있던 이유는 화염 고정 메커니즘의 인자인 전단층(shear layer) 및 연료-공기 주입으로 발생하는 재순환 영역으로 인해 공기역학적인 화염 안정화를 확보할 수 있으며, 적정 운동량 플럭스(momentum flux) 비를 통해 NOx 발생량을 줄일 수 있음을 확인할 수 있었다[16].
비슷한 사례의 연구로 Ayed 등은 APU에 직경 0.3 mm 인젝터를 갖는 MM 버너를 적용한 실험를 통해 화염구조, 유동장 및 온도 분포를 분석하였다. 이를 통해 화염 주위의 냉각 공기 흐름의 조절을 통해 특정 매개변수인 에너지 밀도 및 연료 분사 깊이(y) 와 임계 분사 깊이() 그리고 blockage ratio(BR) 조절을 통해 NOx 배출량을 줄일 수 있음을 관찰했다[17]. Fig. 3는 실험 결과 중 하나로 정규화된 에너지 밀도 6.7 MW/m2·bar일 때 화염 구조와 NOx 배출량을 확인할 수 있다. 전부하 조건의 설계점인 당량비 0.4에서 2 ppmV 미만의 NOx가 배출되었으며, 이를 통해 MM 버너의 성능을 입증하였다. 입증된 성능 결과는 고에너지 밀도로 연소 되는 산업용 가스터빈에도 적용되었으며, 제작 용이성을 고려하여 연료 주입구 직경 1.0 mm의 연소기를 설계하였다. 그 결과 고에너지 밀도 상태에서도 노즐당 열량이 11배 이상 증가되는 것과 낮은 NOx 배출량을 얻는 결과를 보고하였다.
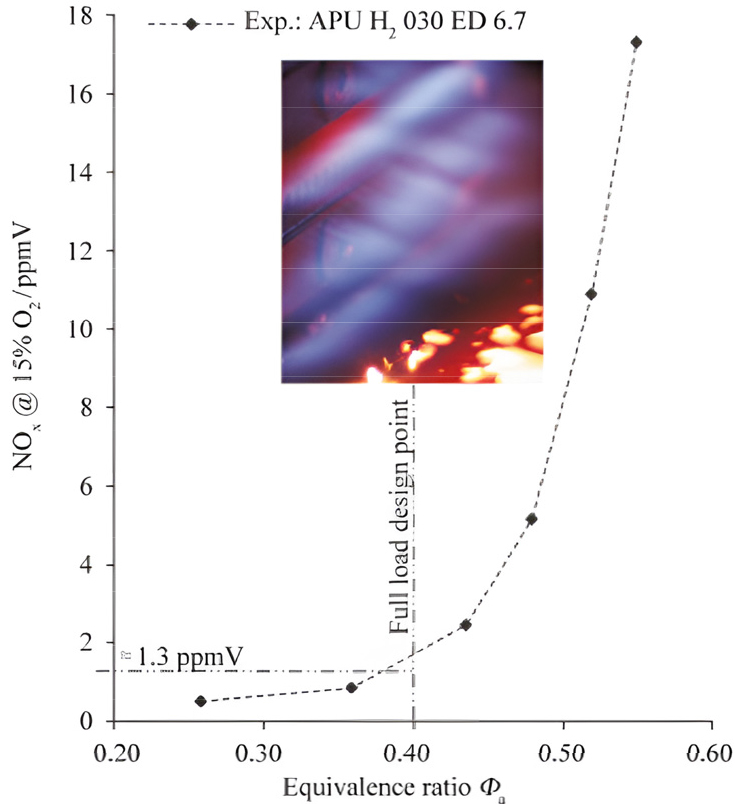
Fig. 3.
Experimental results at an equivalence ratio of 0.4, normalized energy density of 6.7 MW/m2·bar[17].
이 외에도 채널의 직경 변화에 따른 혼합 성능을 확인한 연구 사례도 보고된 바 있다. Chen 등은 예혼합 타입의 길이 55 mm, 연료 주입구 직경 0.6 mm인 단일 MM 노즐을 기준으로 8.4 mm의 채널 직경을 0.2 mm씩 변경하여 혼합 성능을 확인하였다[18]. 채널 직경의 변화는 혼합 성능을 제어할 수 있는 연료와 공기 운동량 비(fuel-air momentum ratio; J)에 영향을 미치는데 직경이 증가함에 따라 운동량 비의 증가와 혼합을 도와주는 vortex 크기의 증가로 연료 jet와 공기의 접촉을 촉진 시켜 혼합 성능이 향상되는 결과를 보였다. 그러나 채널 직경 9.4 mm(J=24.13)일 때 혼합 성능이 크게 감소하는 것을 관찰하였는데, 이는 수소 질량 분율 분포를 나타낸 Fig. 4에서 확인할 수 있는 것처럼 채널의 직경이 커짐에 따라 증가된 운동량 비의 영향으로 연료 제트의 세기도 함께 강해지면서 연료가 공기 흐름을 통과하여 채널 외벽 근처에서 혼합 영역을 형성하게 된다. 이 영향으로 연료 주입구 쪽의 수소 농도는 상대적으로 낮아지게 되고, 공기 흐름과의 혼합 균일도가 감소 되는 것을 확인하였다. 이를 통해 최적의 혼합 성능을 위한 최적의 운동량 비(21.82≤J≤24.17)가 있음을 확인하였으며, 예혼합 타입의 노즐 채널 직경은 9.2 mm(J=23.49)일 때 최적화된 혼합 성능을 가짐을 보고하였다.
위 연구 사례를 통해 연료 주입구 및 노즐의 채널 직경 변화에 따라 유동 특성이 달라지며, 이러한 변화는 운동량 비나 화염 고정 메커니즘 인자인 전단층(shear layer) 및 재순환 영역 형성에 영향을 미침을 확인하였다. 혼합과 화염 형성에 있어 중요 인자인 연료 주입구 및 노즐 채널의 직경은 예혼합 또는 비예혼합 타입의 노즐 설계 시 주요 변수로 고려해야 하며, 노즐에 맞는 최적 조건을 적용하는 것이 필요하다.
2.2.2 연료 주입구 형상에 대한 영향
교차 유동과 관련하여 원형 및 타원형 등 다양한 연료 주입구 형상에 따라 연료와 산화제가 효과적인 혼합이 가능한 연구 결과가 보고되고 있다. MM 연소 시스템 노즐의 경우 혼합 효율성과 연소 안정성 그리고 오염물질 배출제어를 위해 원형인 연료 주입구 형상에 대해 주로 연구 되었지만, 더 나은 혼합 성능과 배출 제어를 위하여 다양한 연료 주입구 형상에 대하여 연구가 수행 중이다.
Chen 등은 원형 외에 예혼합 MM 연소 시스템에서 비원형 연료 주입구에 대한 혼합 성능을 확인하고자 4개의 타원형의 연료 주입구로 구성된 단일 노즐에 대해 연구했다[19]. 연료 주입구의 형상이 타원형에 가까워질수록 연료 분사 초기에만 혼합 성능이 증가하는 것을 확인하였다. 연료가 교차 유동 방식으로 분사될 때 공기 흐름과 함께 혼합층을 형성하며, 유동 흐름의 변화를 주는 일종의 소스(source) 지점과 와류(vortex)가 생성된다. 소스 지점은 연료 주입구 형상이 타원형에 가까워질수록 연료 분사 방향의 근처에서 생성되며, 높아진 연료와 공기의 운동량 비로 인해 추가적인 와류가 생성되므로 연료 제트 흐름을 유지하지 못해 혼합 성능이 저하된다. 관련 내용은 Fig. 5를 통해 확인할 수 있으며, 연료 주입구 형상이 전단층 및 와류 등 혼합 성능과 유동 특성에 영향을 주는 인자임을 보고하였다.
Choi 등은 연료 주입구의 위치 변경을 통해 발생하는 스월(swirl)이 혼합에 영향을 미치는지 조사했다[20]. Fig. 6(a)는 분사 방법에 대한 개략도로 기존의 연료 주입구는 수직형으로 공기 흐름에 교차 유동 형태로 연료를 분사하였다면, 연료 분사 거리를 반경 방향으로 조정한 후 접선 방향으로 분사하여 선회 유동을 형성하였다. Fig. 6(b)는 스월 형성의 영향으로, 분사 거리가 늘어남에 따라 하나의 화염이 4쌍의 작은 화염으로 분리되어 quadruple flame(QF) 구조가 되는 것을 보여준다. 분리된 화염은 화염을 소형화 시키고, dump 면에 고정되어 화염 안정성을 높이는 역할을 하며 반응물의 체류 시간을 감소시킨다. 체류 시간의 감소는 NOx 배출량을 저감 시키는 역할을 한다. 실험을 통해 당량비 0.66과 스월 수 0.1175 이상에서 소형 화염이 형성되고, NOx 형성에 영향을 미치는 반응물들의 체류 시간이 줄어듦과 동시에 NOx 배출량이 감소하는 것을 확인하였다.
이와 비슷한 사례로 Lei와 Kandelwal도 분사 위치 변화를 통해 발생하는 선회 유동을 활용하여 혼합 성능을 개선하고, 연소 온도를 낮춤으로써 NOx 발생량을 30% 이상 개선되는 것을 확인하였다[21]. 또한, 기존의 챔버보다 40 mm 가량 길이를 축소할 수 있으며, 연소기의 소형화를 달성하여 무게에 대한 부담을 줄여 항공용 연소기로 MM 연소 시스템을 적용할 수 있음을 보고했다.
연료 주입구의 형상 변경이 아닌 채널의 형상을 변경하여 혼합 성능과 NOx 배출량을 제어하고자 하는 연구도 진행되었다. Murthy 등은 예혼합 MM 연소 시스템에서 주로 사용되었던 원통형 채널이 아닌 디퓨저 형태의 채널을 제안하였다[22]. 발산 각도 3.7도를 가진 디퓨저 형태의 채널과 기존의 원통형 채널을 비교하였을 때, 디퓨저 형태의 채널에서 형성된 재순환 영역이 채널 출구 쪽으로 이동되는 것과 대칭적인 대류 영역이 형성됨으로써 화염 안정성 및 고정 능력을 확인하였다. 또한, 연소 시 원통형의 모델보다 1900 K 이상의 고온영역이 적은 것을 확인할 수 있는데 이는 열적 NOx 발생량이 최소임을 의미한다. NOx 배출량의 경우 원통형 채널보다 디퓨저 채널 형태가 약 80% 정도 더 감소됨을 보고하였다. 수소, 케로신, 메탄을 포함한 연료 혼합물에 대한 화염 안정성과 NOx 발생량을 조사한 Karakurt 등도 디퓨저 타입의 채널을 이용하였다[23]. 디퓨저 타입의 채널은 화염 안정화를 위한 디자인이며, 인젝터 위치 조정을 통해 각 연료에 대한 화염 특성과 반경 방향 속도를 변경시켜 충분한 체류 시간을 통해 화염을 고정 시키는 장점을 가지고 있다. 그리고 출구에서 재순환 영역을 형성하여 원환형 흐름(toriodial flow)을 유지함으로써, 수소와 메탄 연료의 MM 연소방출 특성 결과인 Fig. 7에서 확인할 수 있는 것처럼, 수소의 경우 희박 조건인 당량비 0.2에서도 효과적인 연소 성능과 낮은 NOx 배출량을 달성함을 보고하였다.
연료 주입구의 형상 변경이 아닌 채널의 형상을 변경하여 혼합 성능과 NOx 배출량을 제어하고자 하는 연구도 진행되었다. Murthy 등은 예혼합 MM 연소 시스템에서 주로 사용되었던 원통형 채널이 아닌 디퓨저 형태의 채널을 제안하였다[22]. 발산 각도 3.7도를 가진 디퓨저 형태의 채널과 기존의 원통형 채널을 비교하였을 때, 디퓨저 형태의 채널에서 형성된 재순환 영역이 채널 출구 쪽으로 이동되는 것과 대칭적인 대류 영역이 형성됨으로써 화염 안정성 및 고정 능력을 확인하였다. 또한, 연소 시 원통형의 모델보다 1900 K 이상의 고온영역이 적은 것을 확인할 수 있는데 이는 열적 NOx 발생량이 최소임을 의미한다. NOx 배출량의 경우 원통형 채널보다 디퓨저 채널 형태가 약 80% 정도 더 감소됨을 보고하였다. 수소, 케로신, 메탄을 포함한 연료 혼합물에 대한 화염 안정성과 NOx 발생량을 조사한 Karakurt 등도 디퓨저 타입의 채널을 이용하였다[23]. 디퓨저 타입의 채널은 화염 안정화를 위한 디자인이며, 인젝터 위치 조정을 통해 각 연료에 대한 화염 특성과 반경 방향 속도를 변경시켜 충분한 체류 시간을 통해 화염을 고정 시키는 장점을 가지고 있다. 그리고 출구에서 재순환 영역을 형성하여 원환형 흐름(toriodial flow)을 유지함으로써, 수소와 메탄 연료의 MM 연소방출 특성 결과인 Fig. 7에서 확인할 수 있는 것처럼, 수소의 경우 희박 조건인 당량비 0.2에서도 효과적인 연소 성능과 낮은 NOx 배출량을 달성함을 보고하였다.
혼합 성능을 위해 새로운 노즐 형상을 개발하는 연구도 진행되었다. Fig. 8은 MM 연소 시스템으로 적용하기 위한 캘리포니아 대학에서 개발한 micro-mixing cup 노즐이다[24, 25]. micro-mixing cups 기술은 예혼합 연소 유형으로 낮은 연소 온도를 통해 NOx 배출을 감소시키는 기술이며, 수소 연료 공급은 노란색, 주황색은 공기 공급 채널이다. 공기는 컵의 가장 자리를 따라 선회 유동이 유도되면서 수소와 혼합이 된다. micro-mixing cups 기술은 뛰어난 확장성과 5 ppm 미만의 낮은 NOx 배출량을 가지는 장점을 가지고 있지만, 제조의 복잡성과 수소 연소에서 가장 중요한 문제인 역화에 있어 3 bar 이상의 가압 조건에서 역화가 발생하는 단점을 가지고 있다.
연료 주입구 형상은 혼합 및 화염 안정화하는데 있어 영향을 주는 인자임을 확인할 수 있었다. 혼합 성능은 와류와 난류에 의해 향상됨을 확인할 수 있었으며, 재순환 영역 또는 전단층의 형성과 화염을 소형화하여 반응물의 체류 시간을 조절함으로써 화염 안정성과 NOx 배출 제어에 영향을 미침을 확인했다. 이는 앞서 확인했던 연료 주입구의 직경 변화의 사례에서처럼 주입구 형상이 유동 특성에 영향을 주는 인자임을 알 수 있었으며, 노즐 설계 시 모델에 맞는 최적화가 필요함을 확인할 수 있었다.
2.2.3 연료 주입구 개수에 따른 영향
MM 연소 시스템에서의 연료 주입구의 개수에 따른 연소 성능과 NOx 배출의 영향을 확인하고자 수행된 연구도 다수 보고되고 있다. 신시내티 대학교의 CFRL(Combustion and Fire Research Laboratory)팀은 PIT(Porous Injection Technology)에 대한 연구를 통해 천연가스 및 합성 연료에 대한 MM 연소 시스템의 인젝터를 개량하였다[26]. 기존의 MM 연료 주입 방식과 달리 주입되는 연료 및 공기에 대한 운동량 플럭스 비를 고려하지 않고 자유류 상태의 공기 흐름에 넓은 표면적을 가지는 다공성 주입구를 통해 연료를 주입하는 방식이다. Fig. 9는 개량된 MM 연소 시스템을 나타낸다. 두 개의 블록으로 나뉘는데 하단 블록에는 공기가 주입되는 8개의 튜브로 구성되어 있으며, 상단 블록은 연료가 주입되는 다공성 튜브와 60˚의 각도로 구성된 입출구로 되어 있다. 연료와 공기가 주입되면 상단 블록의 인젝터 벽과 다공성 튜브 사이의 환형(annular) 공간에서 혼합되어 연소하게 되는데, 기존의 교차 유동(cross- flow)보다 혼합을 제어하는데 용이한 것으로 보고하였다. 연료와 공기의 혼합이 이루어지는 상단 부분은 각 노즐에 다공성 튜브와 직경이 같은 센터 바디를 두어 연료와 공기의 혼합 통로를 구성하게 되는데, 혼합 통로를 고려한 최적 인젝터 직경()은 다공성 튜브의 직경(D) 일 때, 그리고 혼합물이 형성되는 상단 블록의 길이()는 의 6배일 때 가장 최적화된 혼합 성능을 얻을 수 있음을 확인했다. 최적 조건에서 배기가스 NOx 배출량은 4 ppm 이하였으며, 각 인젝터들을 모아 연소기로 구성하였을 때, 각각의 인젝터가 독립적으로 작동 가능함에 따라 디자인 확장성을 장점으로 보고하고 있다.
Fig. 10은 Landry-blais 등이 인젝터 70개와 105개로 구성된 비예혼합 타입의 MM 연소기에 대해 수소와 천연가스를 적용한 화염 구조를 보여준다[27]. 수소와 천연가스의 경우 Da(Damkohler number)가 10 이하이면, NOx 배출은 완전한 예혼합 상태와 가까운 10 ppm 수준인 것을 확인하였으며, Da 수가 10 이상이면, 혼합 불량으로 NOx 배출량이 증가함을 확인하였다. 부가적으로, Da 수가 낮아지면 연소 불안정성이 발생할 수 있으나, 반응성이 높은 수소를 사용할 경우 불안정성이 발생하지 않으며, 100 ms 미만의 최적화된 혼합 시간과 체류 시간을 적용한다면, 안정적인 연소와 적은 양의 NOx를 배출할 것으로 보고하였다.
2.2.4 노즐 주위 Bluff body 및 Baffle의 영향
MM 연소 시스템의 특징은 소형 화염으로 반응물의 체류 시간을 단축하여 NOx 배출량을 최소화 하는데 있다. 이때 연소기 설계자는 화염 안정성과 원하는 화염 길이를 고려해야 한다[28]. 특히 수소의 경우, 빠른 반응성으로 인한 역화 가능성과 자동점화와 같1은 연소 특성으로 인해 화염 및 운용 안정성에 문제가 발생할 수 있어 bluff body 및 baffle을 사용해 불안정성을 조절한다. 부분 예혼합 MM 연소기를 연구한 Scmidt 등은 bluff body의 유무에 따라 NOx 배출량을 비교하는 연구를 수행하였다[29]. Fig. 11은 bluff body 유무에 따른 혼합 성능과 속도장을 비교한 것으로, 교차 유동 형태로 분사되는 수소 노즐에 12 mm 직경을 가지는 원형의 bluff body를 장착함으로써 단면적이 줄어들고, 수소가 공기 흐름으로 유도되면서 혼합 성능이 향상되는 것을 확인하였다. 이는 bluff body가 재순환 영역을 생성함으로 부분적으로 발생할 수 있는 높은 온도 피크를 방지하고 화염 안정성을 향상 시켜, 기존의 노즐보다 NOx 배출량을 40%나 저감 시키는 효과를 확인했다. 또한 수소를 이용한 희박 예혼합 연소기 연구에서 각기 다른 bluff body의 형상에 따라 다른 결과를 보이지만 모두 혼합 성능과 화염 안정성이 향상되는 것을 확인하였다[30, 31].
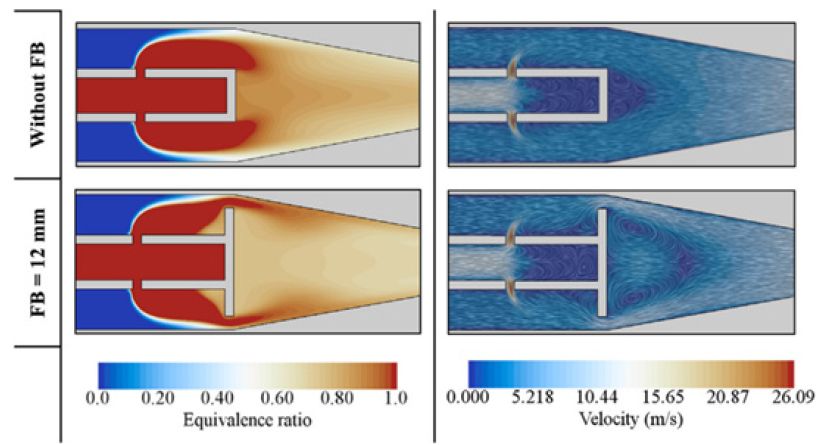
Fig. 11.
Comparison of mixing field (left) and velocity field (right) depending on the presence of a bluff body[29].
bluff body를 화염 고정 등 제어를 위한 방안으로 사용되기도 한다. 아헨대학교에서는 MM 연소 시스템을 대규모 산업용 가스터빈으로 확장하기 위해 에너지 밀도에 따른 연소 효과를 확인했다[32]. 공기 흐름을 유도하는 패널의 설계에 따라 화염을 고정하는 재순환영역의 위치와 그에 따른 NOx 발생량의 변화를 관찰하였다. bluff body의 적용은 혼합 성능 향상 및 NOx 배출 제어 뿐만 아니라 화염 고정 또는 분리가 가능하도록 제어할 수 있음을 확인하였다. 혼합 성능을 높이기 위해 baffle을 사용하기도 한다.
baffle은 bluff body와 같이 재순환영역 및 유체 흐름의 와류(vortex)를 형성하여 혼합 성능을 높이지만, 연료 노즐 또는 연소기 내부에 별도로 장착해주는 장치이므로 bluff body와는 차이가 있다. 기존의 baffle 판의 경우 원형의 홀(hole)로 구성이 되어 연구되었다면[33], 비원형을 채택하여 연구를 진행한 사례도 있다. Kim과 Park은 Fig. 12처럼 baffle 판에 원형과 더불어 사각형과 삼각형의 홀을 이용하여 혼합 및 연소 효율을 확인하였으며, 기준이 되는 원형 baffle보다 비원형 홀이 강한 재순환영역을 형성하여 연소 효율이 향상되는 결과를 확인했다[34].
bluff body와 baffle은 혼합 성능을 증대시킬 수 있으며, 화염 제어에 있어서도 효과적이다. 복잡한 형상과 제작이 MM 연소 시스템에 적용하는데 있어 어려움이 있을 수 있으나 연소 성능이나 제어를 위해서 고려할 수 있다.
2.3 Multi-nozzle Micromix combustor
본 절에서는 MM 원리가 적용된 다수의 단일 노즐들을 하나의 연소기로 통합한 복수 노즐형(Multi-nozzle) MM 연소기에 대해 소개하고자 한다. Fig. 13은 개발 또는 연구 중인 복수 노즐 MM 연소기들의 개념을 보여준다[35]. NASA, Hitachi, Paker Hannifin 그리고 GE에서 MM 연소 시스템을 적용 개발 중인 연소기들로 앞서 확인한 인자들을 최적화하여 수소 전소 및 혼소에 대한 실험을 진행하였다. 단일 노즐들의 통합인 복수 노즐형 MM 연소기는 연료 유연성과 역화 방지가 용이하고, 연소 성능에 영향을 미치지 않고 다양한 크기의 연소기를 설계할 수 있다는 장점이 있어, 차세대 가스터빈 엔진에 수소를 적용할 목적으로 개발 중에 있다.
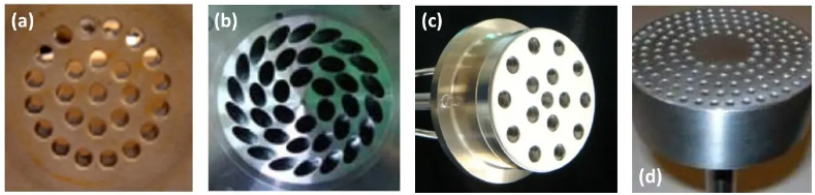
Fig. 13.
Multi-nozzle (tube) micromix combustor concepts, (a) NASA, (b) Hitachi, (c) Paker Hannifin, (d) GE Gas Power[35].
개별로 운용되는 노즐의 개수 변화가 미치는 영향에 대해서 연구를 진행한 Hasemann 등은 동축 유동(co-flow) 형식의 단일 노즐을 6개와 12개의 노즐로 구성된 연소기의 비교 실험을 진행하였다[36]. 혼합 영역 채널의 직경과 길이, 연료 분사 직경 등 동일한 조건이 적용된 노즐을 이용하여 실험을 진행한 결과, 노즐 개수를 2배로 늘렸을 경우, CO 배출이 약 10 ppm 이상 감소함을 확인하였으며 NOx 배출량 역시 저감되는 것을 확인하였다. 이는 노즐의 개수가 많아지면서 공기와 연료의 혼합 성능이 향상되는데, 노즐 유동으로부터 형성되는 전단층이 연소기의 벽 쪽으로 편향되어 연소실 내부의 뜨거운 배기가스와의 혼합을 증가시키기 때문이다. 이로 인해 12개의 노즐 구성이 6개의 노즐 구성보다 혼합 시간이 더 짧지만, 낮은 CO 및 NOx 배출량을 가지게 된다. 또한, 적용된 노즐이 많을 경우, 화염 위치가 노즐 출구면에 더 가깝게 부착되면서 연소 효율이 증가하고, 동시에 화염이 소형화되어 NOx 형성의 매개변수 중 하나인 반응물의 체류 시간이 짧아져 긍정적인 효과가 있음을 보고했다. Liu 등은 중앙의 1개 노즐과 6개의 노즐이 육각형의 벌집 모양으로 배치된 연소기에 수소와 메탄의 혼합연료를 사용하여 배출 특성을 확인하였다[37]. 단열 화염온도 1920 K 조건에서 수소함량이 60%를 초과하지 않는 경우, 10 ppm 이하의 NOx와 6 ppm 이하의 CO가 배출이 되는 것을 보고하였다. 또한 실험을 진행한 모든 조건에서 역화 위험과 화염 안정성을 방해하는 연소 진동이 발생하지 않는 결과를 얻었으며, 설계된 복수 노즐형 MM 연소기의 활용 가능성을 확인하였다. 동시에 높은 수소 함량 조건에서는 화염 안정성을 위해 노즐간의 거리와 열적 부하에 대한 영향을 분석하는 등 추가적인 실험의 필요성을 보고하였다.
Xing 등은 1.15 MW급의 H-class의 가스터빈에 역화 방지를 위해 연구한 테이퍼형 MM 노즐 40개를 적용한 prototype MM 연소기를 개발하였다[38]. 해당 연구에서 40개의 노즐은 연소 가스 온도의 균일성 향상과 NOx 제어를 위한 목적으로 4개의 그룹으로 나뉘어 배치되었다. 연료 온도 473 K에서 prototype MM 연소기는 99.99%의 연소 효율과 13.55 ppm의 낮은 NOx 배출 등 우수한 연소 성능을 보였다. 또한 Liu 등은 MILD 연소기와 복수 노즐형 MM 연소 시스템의 비교 실험을 통해 복수 노즐형 MM 연소기의 잠재력을 확인하였다[39, 40]. 직경 5 mm, 길이 10 mm의 microscale 노즐 24개가 배열된 복수 노즐형 MM 연소기는 혼합 영역, 역화 방지 영역, 가스 분배 영역으로 구성되어 있다. 수소와 메탄 혼합물을 사용하여 수소함량의 변화(0~40%)에 따른 비교 실험 결과, 수소함량 40% 일 때 복수 노즐형 MM 연소기가 MILD 연소기보다 안정적인 연소를 유지하기 위한 음향 한계(acoustic limit)과 희박 화염 날림(lean blowout, LBO)의 한계가 380%로 확장되는 우수한 연소 안정성을 보였다. 하지만 MILD 연소기와 비교하여, 복수 노즐형 MM 연소기에서 NOx 배출량이 약 2 ppm 높은 것으로 보이는데, 이는 MILD 연소기의 특성인 연소기 내부에서의 무화염 연소 상태를 유지하는데 필요한 배기가스의 재순환으로 인해 약간의 차이가 발생한 것으로 확인된다. 그러나 복수 노즐형 MM 연소기 또한 전반적으로 10 ppm 이하의 낮은 배출량이 확인됨으로써 연소 안정성과 더불어 배출제어에도 효과적인 것으로 입증되었다. 또한, 40% 이상 고농도의 수소를 연료를 사용할 경우 복수형 노즐 연소기의 안전성을 고려하여 역화 방지를 위해 최소 화염 부상 거리를 제시하였으며, 단일 microscale 노즐 내경의 1.6배 이상의 화염 부상 거리를 가져야 복수형 노즐 MM 연소기를 제작 시, 역화로부터의 연소기 안정성 및 낮은 NOx 배출량 그리고 높은 연소 성능을 가질 수 있음을 보고하였다.
Fig. 14는 NASA에서 개발한 Glenn multi-tye LDI N1 연소기로 길이 6.35 mm 튜브와 연료 주입구 직경 0.508 mm로 구성된 단일 노즐 25개로 구성되어있다[12,42]. Fig. 14(a)의 N1은 교차 흐름 형식으로 수소를 180˚ 간격으로 위치한 연료 주입구에서 분사하여 짧은 혼합 영역을 생성하도록 설계되어 있다. Fig. 14(b)의 C1 구성은 로켓 엔진의 분사 기술을 기반으로 중앙에 “+” 모양 수소를, “+” 모양 주위로 여덟 개의 각도로 공기를 분사하도록 설계되었다. Fig. 14(c)의 C2의 구성은 N1 인젝터와 설계는 유사하지만, 원형 대신 삼각형으로 구성되어 있는 차이점이 있다. 삼각형 각 변의 가장자리에서 수소를 분사하는데, 이는 N1과 동일한 공기 흐름 영역을 유지하면서 요소의 패키징을 극대화할 수 있는 개념이다. 이를 이용하여 삼각형이 크기를 줄이게 되면 추가적인 수소 분사 지점을 만들어 공기 유동 흐름에 수소 첨가를 증가시킬 수 있고 혼합을 촉진할 수 있는 장점을 가진다. Fig. 14(d)의 C3와 C4는 현재 이용 중인 가스터빈 기술을 접목한 디자인으로 C4는 각 홀의 중앙에 단일 수소 노즐을 사용하고, 대량의 선회 유동을 발생시킴으로써 혼합을 생성한다. C4의 구성은 C3를 기반으로 하지만 중앙 홀을 4 방향의 방사형 수소 유동으로 대체되는 차이점이 있다. 수소 가스터빈 엔진의 잠재력을 탐색하기 위한 방안으로 시작된 LDI(lean direct injection) 구성의 4가지 디자인에 대해 시험을 한 결과, 성능이 우수하며 안정성을 확인하였다. 또한, 낮은 수준의 NOx 발생량과 역화 및 자동점화 등 연소 불안정성과 관련된 현상이 발생 되지 않는 것을 확인하였다. C4 디자인의 경우, 다른 디자인들에 비해 당량비 0.3보다 낮은 당량비에서도 NOx와 내구성이 가장 우수함을 확인하였다. 이를 통해 MM 방식과 선회 유동 형성이 화염 안정성 등 연소 성능과 NOx 배출 제어에 있어 용이한 것으로 보고되었으며, 고출력 터빈 연소기로 구현할 수 있어 MM 연소 시스템의 잠재력을 확인하였다.
Fig. 15는 아헨대학교의 Funk 등은 예혼합 연소기의 문제점인 자동점화 및 역화의 위험을 방지하고 연소 안정성과 NOx 생성을 최소화하기 위하여 비예혼합 MM 원리를 적용하여 개발한 연소기를 보여준다[14, 15, 16, 17]. MM 연소기는 버너의 주요 단면에 균일하게 분포된 매우 소형화된 확산 화염으로 구성된다. 이 소형 화염은 연소 영역에서 반응물의 체류 시간을 줄여 NOx 배출량을 낮게 조절하며, 교차 유동 방식으로 설계되어 혼합 공정을 향상 시킨다. 특히 화염 고정은 NOx 배출 특성에 있어 큰 영향을 미치는데 이를 제어하기 위하여 MM 버너 구조 내 재순환 구역 및 와류에 영향을 미치는 교차 유동의 운동량 플럭스 비를 최적화시키는 것이 중요한 것으로 보고하였다. 1600개의 소형 인젝터로 구성된 환형의 연소기는 에어버스 A320 같은 다양한 항공기의 보조 동력 장치(Auxiliary power unit; APU)인 GTCP36-300에 적용하기 위해 개발되었으며[9], 항공기 외에 산업용의 가스터빈에도 적용을 위해 에너지 밀도를 높이는 실험도 진행했다. 여러 실험 조건 및 수치해석을 통한 연구 결과, 역화에 대한 강점과 수소 연소에 있어서 안정성을 입증할 수 있었으며, 특히 노즐 직경 0.84 mm일 때 최적화된 연소 챔버의 설계가 도출되었다. 개발 초기의 0.3 mm 설계와 비교 시 노즐 당 열 출력은 약 390% 증가와 99% 이상의 연소 효율 및 4 ppm 이하의 낮은 NOx 배출량을 보이면서 MM 연소기가 차세대 가스터빈의 연소기로서의 가능함을 입증하였다[15,42,43].
2.4 Micromix combustion instabilities
연소 불안정성은 연소 과정에서 불규칙하거나 예측할 수 없는 진동(oscillation) 또는 열음향학적(thermoacoustic) 영향으로 인해 발생된다. 이러한 연소 불안정성을 제어되지 않는 상태로 두면 구성요소 진동, 열 전달 속도 증가, 화염분출(blow-off) 그리고 역화와 같은 결과를 초래할 수 있다. 시간이 지남에 따라 진동은 엔진의 작동 범위를 제한하면서 상당한 시스템 성능 저하 및 구조적 손상으로 이어지는 최악의 상황에 직면하게 된다.
Lee 등은 축소된 산업용 GE7EA 가스터빈 부분 예혼합 연소기를 사용하여 메탄-수소 합성가스 화염에 대한 self-excited 열 음향 불안정성에 대해 연구했다[44]. 연료 열량 40 kW 및 50 kW에서 운용되는 연소기에 혼합연료 수소 첨가를 0~100% 사이로 변화를 주어 확인하였다. 40 kW 조건에서 수소함량 30~80% 사이일 때 고주파 연소 불안정성이 발생하였으며, 50 kW로 증가시키면 연소 진동의 강도가 증폭되는 동시에 연소 불안정성을 유발하는 수소함량 범위가 약 5~100%까지 확장됨을 확인했다. 연료의 수소함량이 증가함에 따라 고주파수 음향 모드가 활성화되는 것을 관찰하였고, 고주파수 불안정성의 여기를 포함한 연소기의 고유 주파수 사이의 모드 전환이 촉발될 수 있음을 확인하였다.
Wicksall과 Agrawal은 예혼합 연소기를 이용하여 다양한 단열 화염 온도 범위에서 수소함량이 최대 40%로 혼합되는 메탄-수소 연료에 대한 연소 불안정성을 실험적으로 연구했다[45]. 대기압 조건에서 진행된 실험을 통해 수소함량이 증가 될수록 연소기가 열 음향적으로 불안정함을 관찰하였다. 수소 혼소에서 수소함량의 증가는 동적 불안정성 영역이 더 낮은 당량비로 이동되도록 하며, 이에 따라 화염의 위치와 속도의 변화를 통해 연소기의 열 음향 특성이 변경될 수 있음을 확인하였다.
Lee와 Kim은 60개의 복수 노즐로 구성된 MM 연소기를 이용하여 희박 예혼합 수소 전소 화염과 메탄 화염 사이의 화염 역학의 주요 차이점을 확인하기 위해 self-excited 연소 불안정성을 조사하였다[46]. 200°C의 입구 온도와 유속이 25 m/s 고정된 조건에서 99.9% 와 99.9% 의 화염에 대해 연구하였다. 연소기 길이 변화에 수소 화염은 1 kHz의 고주파수 불안정성을 포함하여 여러 고차의 음향 모드가 활성화되는 것을 확인하였으며, 메탄 화염의 경우 310 Hz 이하의 저주파 모드에서만 불안정성을 나타내며 수소 화염에 비해 상대적으로 낮은 진폭을 보였다. OH PLIF 화염 이미지인 Fig. 16(a), (b)는 두 화염이 극한 주기 진동 동안 극도로 다르게 진동함을 보여준다. 수소 화염은 화염 간의 상호 작용 없이 연소기 출구 근처에서 개별적으로 진동하지만, 메탄 화염은 하나의 대규모 전역 진동을 형성하기 위해 버섯 모양처럼 합쳐져 진동하는 것을 관찰하였다. 이러한 분석을 통해 MM 타입의 인젝터 배열에서 희박 예혼합 수소-공기 화염의 행동 패턴을 설명하고 자발적 불안정성의 발생 맵핑을 수행하였다.
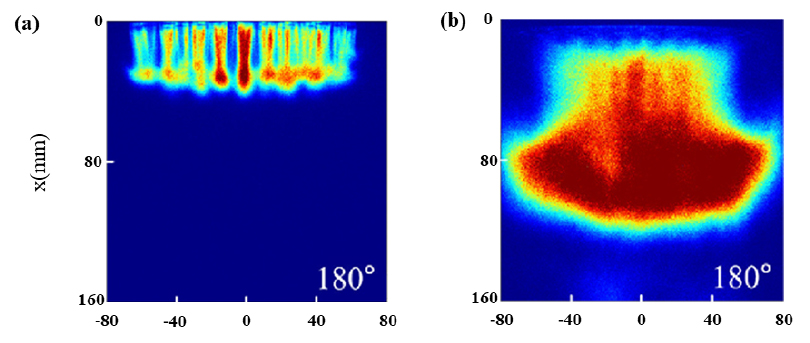
Fig. 16.
OH* chemiluminescence images for (a) hydrogen and (b) methane flames at a constant adiabatic flame temperature of 1881 K (reformed) [46].
Cao 등은 수소 전소 MM 연소 시스템에서 증기 희석이 화염 주파수와 진동 특성에 미치는 영향을 조사하였다[47]. MM 버너는 8개의 연료 주입구와 튜브 내벽의 24개의 사선 주입구에서 산화제와 희석제가 주입되며, 스월 수 0.5, 출구 속도 55 m/s 그리고 레이놀즈 수 20,000 고정 조건에서 화염 불안정성 특성에 대한 당량비와 증기 희석비의 영향을 확인했다. FAZ(flame arm zone)에서의 진동 주파수 스펙트럼 분석 결과, 당량비의 증가가 열 방출 및 고조파(harmony) 주파수 강도에 영향을 주며, 이러한 영향은 열 방출 영역이 blue-shift 됨과 동시에 화염 길이의 연장으로 주파수가 저주파 영역으로 이동하게 된다. 또한 증기 희석비의 증감은 진동의 강도와 위치에 영향을 주며, 희석비 25%일 때 주기적인 열 음향 진동이 쉽게 발생함을 확인하였다. 스펙트럼 분석 외에 불안정성의 성장을 확인하기 위해 실시한 DMD(dynamic mode decomposition) 비교 분석 결과, 열 음향 진동이 발생하는 저주파수 영역에서의 화염구조가 일관된 모습임을 확인하였으며 당량비 및 희석비에 따른 FAZ에서의 진동 위치와 강도 변화를 확인한 스펙트럼 분석 결과와 일치함을 보였다. 이를 통해 당량비와 증기 희석이 MM 연소에 미치는 진동 특성과 구조를 확인할 수 있었으며, 주파수 스펙트럼 분석 방법과 DMD 방법이 연소 불안정성을 보다 정확하게 분석 가능함을 입증했다.
McClure 등의 연구에서는 교차 유동 방식을 적용한 노즐을 사용하여 수소 전소 MM 확산 화염의 강제 반응을 수치적인 방법으로 연구했다[48]. 정상 상태 RANS 해석을 통한 FTF(flame transfer function) 결과, 2,000 Hz 이상의 매우 높은 주파수까지 FTF 이득이 실질적으로 감소하지 않음을 확인했다. 이는 천연가스를 연소하는 기존의 희박 예혼합 연소기의 일반적인 FTF 관측과 차이가 있으며, 수소 화염이 더 넓은 범위의 주파수에 걸쳐 열 음향 진동을 증폭할 수 있음을 확인하였다. 또한 수소 MM 연소기가 고주파 연소 불안정성에 있어 더욱 취약할 수 있음을 보였다. 수소 전소를 목적으로 한 MM 연소기 운용은 높은 주파수의 연소 불안정성을 유발할 수 있는 잠재력이 있으며, 연소 진동을 완화하는 방법을 강구하지 않으면 연소기 하드웨어 에 피해를 초래할 수 있음을 지적했다[49].
3. Micromix 연소기 실용 사례
본 절에서는 가스터빈 제조사들이 MM 연소 시스템을 적용한 연구개발 사례들을 소개하고자 한다.
Fig. 17은 MITSUBUSG-HITACHI에서 개발 중인 멀티 클러스터(multi-cluster) 연소기이다. 역화 방지와 연료 유연성을 확보하기 위해 개발된 멀티 클러스터 연소기는 동축 또는 교차 유동이 되도록 일정 수의 연료 노즐과 산화제 주입구를 가지는 클러스터들로 구성되어 있다[50,51]. 중앙에 파일럿 버너가 있고 그 주변으로 6개의 메인 버너로 구성된 연소기는 파일럿 버너에 초기 점화를 유지하기 위한 기름 또는 합성 가스가 분사되며, 메인 버너는 연료가 중앙에 위치한 상태에서 산화제인 공기가 분사되어 선회 유동을 형성한다. Fig. 17(b)는 메인 버너의 개략도와 중심선을 따라 압력 프로파일과 연소기의 형상을 나타낸 것이다. 선회 유동을 형성하는 다공판(perforated plate)이 축소-확산 형상으로 설계됨에 따라 축소 형상에서의 유동은 선회 반경이 감소됨에 따라 회전 속도가 증가되면서 유리한 압력 구배를 유발하고, 확산 영역의 유동은 선회 속도의 감소로 인해 역압력 구배를 유도한다. 이러한 역압력 구배가 연소 가스의 재순환을 유발하는 역할을 한다. 결과적으로 메인 버너의 각각의 클러스터는 Fig. 17(a)와 같이 부상된 원뿔 형상의 화염을 형성하여 역화 방지와 NOx 제어에 이점이 있음을 확인하였다. HITACHI의 연소기는 예혼합 연소의 장점과 역화 방지 및 확산화염의 장점을 결합한 연소기로 시험 결과 10 ppm 미만의 낮은 NOx 배출량을 유지할 수 있었으며, 수소의 함량이 높아질수록 더 나아진 성능을 보임을 보고하였다. 현재 HITACHI의 연소기는 수소함량 30% 혼소 실험을 실증 완료하였으며, 수소 전소를 위한 실증 실험을 진행할 예정이다.
Fig. 18은 Parker Hannifin과 Georgia Tech의 공동 연구로 개발한 MM 연소 시스템이 적용된 희박 예혼합 가스터빈의 multi-point 인젝터이다[52]. 수소 및 혼합가스를 위한 것으로 1차 주 모듈(primary module)에는 7개의 믹싱 컵으로, 2차 모듈(secondary module) 모듈에는 12개의 믹싱 컵으로 구성되어 있다. 희박 조건에서의 운용성능을 향상을 확인하고자 실시한 주 모듈과 2차 모듈의 단차를 둔 실험 결과, 연료 흐름의 단계별 분사 구분과 주 모듈 보호 기능을 통해 화염의 안정성이 향상됨을 확인하였다. 또한, 연소 제어 시스템에 피에조 밸브 기술을 도입하여 고대역폭인 500 Hz에서의 운전 가능한 연료 밸브 시연을 통해 동적 안정성을 향상시켰다. 피에조 밸브 기술 도입이 화염 역학, 열 방출, 음향 특성에 변화를 줄 수 있음을 입증하였다.
Fig. 19는 GE에서 설계한 DLN 2.6e multi-pipe mixer system 연소기와 수소함량의 차이에 따른 연소 형태를 보여준다. 산화제인 공기가 병렬로 배열된 여러 개의 채널을 통해 흐르게 되고, 연료 플레넘이 채널을 둘러싼 형태의 이 연소기는 연료인 저탄소 혼합가스를 교차 유동 혼합 방식을 활용하여 방사형으로 주입된다[8,53]. LDI(Lean direct injection)와 유사한 디자인이지만, 연료 노즐 내부에 수소와 질소 등 혼합을 위한 예혼합 영역이 있다는 차이점이 있다. 튜브 내 공기 속도는 혼합물의 화염 속도보다 높게 설정하여 고 수소함량의 혼합물에서도 역화의 위험을 방지할 수 있으며, multi-pipe mixer의 짧은 길이와 직선 흐름 경로로 인해 3.5% 정도의 낮은 압력 강하로 운전 안정성을 달성할 수 있는 것으로 보고되었다. multi-pipe mixer로 구성된 full-can 형식인 DLN 2.6e 버너는 H급(수소함량 50% 혼합가스) 및 F급(수소함량 60%-질소 40% 혼합가스) 조건의 가스터빈 환경에서 시험을 통해 오염물질 배출 면에서 매우 우수한 성과를 보였다. F급 조건의 환경시험에서는 NOx 배출량이 10 ppm 이하임을 확인했으며, 추가적인 질소를 20% 추가할 경우 3 ppm 이하의 NOx 수준을 보고하였다. 또한, 90%의 수소함량을 가지는 고농도 수소 연료를 사용하여 100시간 이상의 운용 실험을 통해 안정성도 확보하였다. 이를 통해 교차 유동 방식의 혼합이 고농도의 수소 연료를 사용하는 연소기에 적합함을 확인하였고, multi-pipe mixer 시스템 연소기가 저 NOx 제어에 용이하고, 고급 가스터빈 시스템에서 수소를 연소 시키는데 효과적임을 입증하였다.
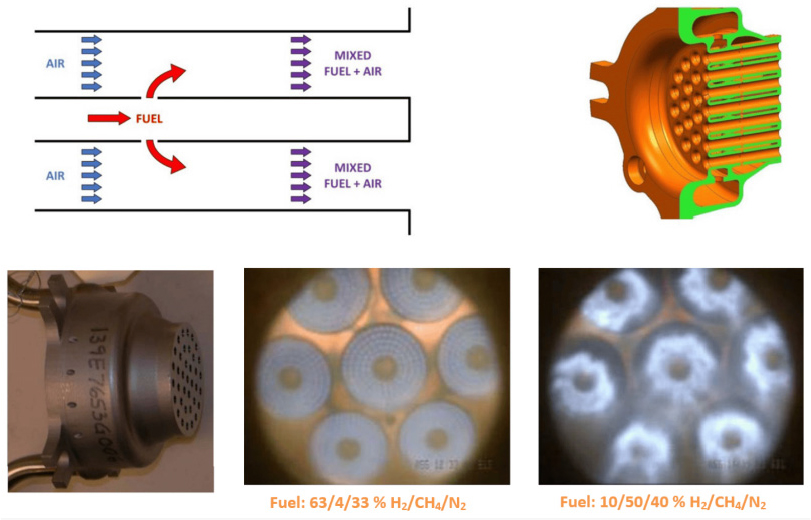
Fig. 19.
GE multi-pipe system DLN 2.6e combustor and photograph of small multi-pipe mixer for high-hydrogen fuel[53].
Fig. 20은 KHI(Kawasaki Heavy Industries)의 M1A-17 가스터빈 연소기를 보여준다. LDI 형식의 예혼합 방식을 사용한 다른 제조사와 다르게 M1A-17은 확산 화염을 이용한 비예혼합 형식의 연소기이다[54]. M1A-17 연소기는 세계 최초로 100% 수소 연료 가스터빈 실증을 일본 고베에서 성공적으로 마친 연소기로써 아헨대학교의 MM원리가 적용[14, 15, 16, 17]되었다. jet in cross-flow 구성으로 공기 흐름에 수직으로 수소가 주입되며, 혼합물이 형성하는 내부 및 외부에 형성된 재순환 영역에 의해 화염이 안정적으로 고정이 된다. 화염 모양과 길이 그리고 NOx 생성에 영향을 미치는 매개변수인 공기 유동의 blockage ratio와 연료 흐름 내부로의 침투 깊이를 이용하여 화염을 소형화시키고, 미세 화염 영역에서 반응물의 짧은 체류 시간을 유도해 낮은 NOx 배출량을 보여준다. 공개된 정보에 따르면, M1A-17는 1.1 MWe의 전력을 공급하고, 약 2.8 MWt의 사용 가능한 열 전력(thermal power)을 가지며, 27%의 전기 효율을 가지고 있음을 보고되고 있다. 실증간 모든 작업 부하에서 M1A-17은 20 ppm의 낮은 NOx 배출량을 유지함으로써 MM의 가능성과 확장성을 확인하였으며, 수소 가스터빈 적용에 있어 효과적임을 보고했다.
4. 결 론
본 연구에서는 수소 또는 수소 기반 혼합 가스가 적용된 MM(micromix) 연소 시스템의 설계 개념이 연소 특성 및 버너 성능에 미치는 영향을 분석하였다. 주요 형상 설계 인자가 MM 연소기에 미치는 영향을 분석하고, 실제 시스템에 적용하기 위한 연구 사례와 MM 연소 시스템에서 발생할 수 있는 연소 불안정성에 대해 조사하였다.
MM 연소기의 최적 성능을 위한 설계 인자들에 대한 연구는 주로 혼합 성능과 화염 안정화, 오염물질 저감을 목적으로 진행되었다. 대부분의 연구에서는 1 mm 이하의 연료 주입구 직경을 적용하고 있으며, 0.3~1.0 mm 사이의 직경이 최적 혼합 성능과 수 ppm 수준의 저 NOx 배출 결과를 갖는 것으로 나타났다. 여기에 타원 형상의 연료 주입구나 디퓨저 형상의 채널을 적용하는 것도 NOx 배출을 저감하는데 도움이 되는 것으로 보고되었다. 연료 주입구의 개수 역시 화염 안정성과 NOx 저감에 영향을 미치지만, 개수의 영향보다는 연료와 공기의 혼합 시간이 NOx 저감에 직접적인 영향을 주는 것으로 확인되었다. 높은 반응성을 가지는 수소 연소 시, 100 ms 미만의 혼합 시간을 적용하는 것이 화염 안정성과 최소 NOx 배출을 위해 적절한 것으로 파악된다. 이 외에도 bluff body 및 baffle도 재순환 영역과 전단층 형성을 통해 효과적인 혼합 성능과 화염 안정화에 도움이 되는 것으로 확인된다. 이러한 MM 노즐들을 통합한 복수 노즐형 MM 연소기들은 가스터빈 연소기에 적용하는 것이 가능하며 다양한 형상의 연구 사례가 보고되고 있다. MM 연소기술에서의 연소 불안정성에 대한 연구는 연소기에서 발생할 수 있는 진동 특성 및 구동 메커니즘을 파악하는데 중점을 두었다. 수소의 연료 특성상 당량비와 증기 희석비 등 매개변수의 영향으로 화염구조 변화와 저주파부터 고주파까지 다양한 주파수 영역에서의 연소 불안정성을 확인했으며, 보다 정확한 분석을 위한 주파수 스펙트럼 분석 외에 DMD 분석 등 다양한 분석 방법을 적용한 연구가 진행 중이다.
MM 연소 시스템에서의 다양한 형상 인자들은 유동 특성에 큰 영향을 미친다. 운동량 비에 따른 재순환 영역, 전단층 그리고 와류 등의 변화가 혼합 성능 및 화염 안정성, NOx 제어에 관여하는 것으로 나타난다. 이러한 요소는 화염 소형화와 짧은 반응물의 체류 시간 등을 유도함으로써 화염 및 운용 안정, 낮은 NOx 배출량에 기여하며, 동시에 수소 연소의 문제점인 역화 및 자동점화 등을 효과적으로 방지할 수 있다. 또한 연소 불안정성에 대한 구동 메커니즘의 확보 등 이상의 연구 결과들로 하여금 연소기의 설계 용이성과 연료 유연성 및 기존의 가스터빈 엔진과의 호환성 등의 장점을 보이며, 실제 연소기에 적용될 수 있는 가능성을 보이고 있다.
에너지 수요와 환경오염이라는 문제 대응에 수소 가스터빈은 큰 대안이 될 것으로 예상되며, MM 연소 시스템은 수소 연료 적용에 있어서 가장 적합한 기술 중 하나로 평가되고 있다. 향후, 국내에서도 비예혼합 타입을 포함하여 다양한 인자들에 대한 지속적인 연구와 함께, 실용적인 적용 방법에 대한 고민이 필요할 것으로 생각된다.